在工业4.0与人工智能技术深度融合的背景下,"炼金"这一古老的概念被赋予了全新的内涵。现代智能炼金工厂通过整合物联网、大数据分析、机器学习及自动化控制技术,实现了从传统化学工艺向高效、精准、可持续制造的跨越式升级。将深入剖析此类工厂的核心工艺逻辑与技术架构,并探讨其创新实践对产业发展的深远影响。
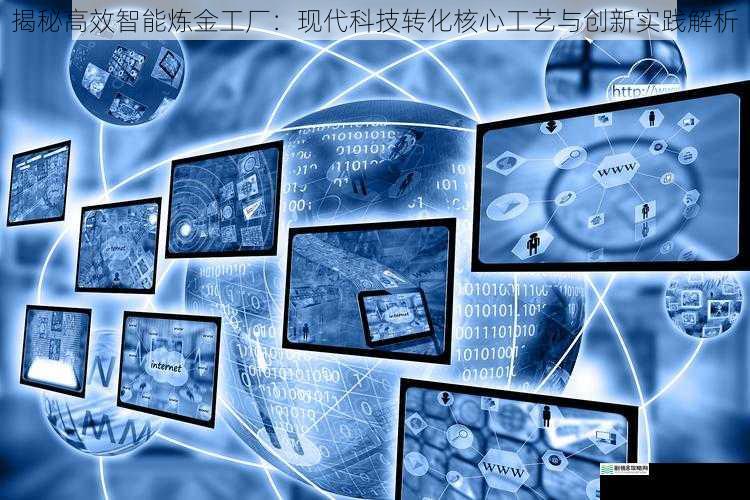
智能炼金工厂的工艺革新逻辑
传统化学制造过程依赖经验驱动的手动调控模式,而智能炼金工厂构建了"感知-分析-决策-执行"的闭环体系。通过高精度传感器网络实时采集反应釜温度、压力、物质浓度等关键参数,结合光谱分析仪与质谱联用装置,系统可精确追踪分子层面的动态变化。例如,在贵金属催化反应中,基于原位表征技术的数据流可实时修正反应路径,将催化剂选择性提升15%-20%。
工艺优化的核心在于机器学习模型的深度应用。通过历史生产数据训练出的神经网络,可预测不同原料配比下的反应动力学曲线,并自主生成最优操作参数。某稀土分离项目通过建立多目标优化模型,在保证纯度99.99%的前提下,将能耗降低23%,废液排放量减少40%。
技术架构的三大创新支柱
1. 动态配方优化系统
依托数字孪生技术构建的虚拟工厂,可在投产前模拟超过200种工艺路线。当原料批次出现波动时,自适应算法能在10秒内调整催化剂用量与反应温度,确保产品质量稳定性。宝钢集团引入的合金冶炼AI控制系统,成功将成分偏差控制在±0.03%以内。
2. 全流程自动化集群
从原料预处理到产物纯化,智能机械臂与AGV物流系统实现无缝衔接。德国巴斯夫试点工厂采用激光诱导击穿光谱(LIBS)在线检测装置,配合自主决策的分馏塔调控模块,使精馏效率提升34%。
3. 绿色工艺重构体系
通过量子化学计算筛选原子经济性更高的合成路径,结合超临界流体技术、微波催化等创新手段,推动清洁生产。杜邦公司开发的生物基尼龙合成工艺,利用酶催化剂在常压下完成聚合,碳排放量仅为传统工艺的17%。
产业变革的实践突破
在贵金属回收领域,智能炼金技术展现出革命性潜力。金田集团建设的电子垃圾提金工厂,通过X射线荧光光谱与卷积神经网络识别废料成分,配合选择性浸出-电积工艺,将黄金回收率提升至98.7%,同时将酸耗量降低62%。
新材料开发周期也因智能系统大幅缩短。华为联合中科院研发的固态电解质材料,借助高通量实验平台在三个月内完成1265组配比测试,筛选出离子电导率突破5mS/cm的创新结构,较传统研发模式效率提升8倍。
挑战与未来演进方向
尽管取得显著进展,智能炼金工厂仍面临多重技术瓶颈。微观反应机理的数据采集精度需提升至飞秒级时间分辨率,多物理场耦合模型的算力需求呈指数增长,这对边缘计算设备的部署提出更高要求。工艺知识库的构建需要打破行业数据壁垒,建立统一的标准体系。
展望未来,量子计算有望在分子模拟领域带来颠覆性突破。谷歌量子AI实验室已实现12量子比特模拟催化剂表面吸附过程,这将推动催化反应设计进入"原子级定制"时代。基于生成式对抗网络(GAN)的材料发现平台,或将在未来十年帮助人类解锁超过5万种新型功能材料。
智能炼金工厂的崛起标志着化学制造从经验科学向数据科学的范式转移。这种转变不仅体现在生产效率的量级提升,更深刻改变了人类探索物质转化的方法论。随着5G通信、数字孪生、自主实验室等技术的持续融合,一个更智能、更清洁、更具创造力的新制造时代正在加速到来。中国作为全球最大制造业国家,亟需在工艺算法、核心装备等领域加强原始创新,方能在新一轮产业变革中占据战略制高点。